Карманный справочник технолога-инструментальщика
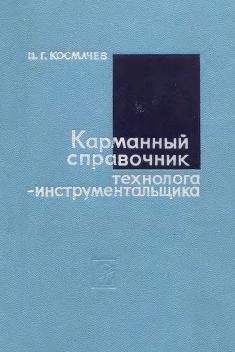
Космачев И.Г.
Машиностроение, 1970 г.
ПОДГОТОВКА ТВЕРДОСПЛАВНЫХ ПЛАСТИНОК И КОРОНОК К СБОРКЕ
Перед напайкой пли механическим закреплением пластинки и коронки проходят подготовительные операции — очистку, шлифование, доводку и сортировку.
Очистка пластинок. Окалину с пластинок твердого сплава удаляют счисткой в галтовочном барабане. Для сокращения времени очистки галтовочный барабан заполняют мелкой абразивной крошкой или крупным речным песком.
Очистка пластинок от окалины происходит в такой последовательности:
а) очистка в галтовочном барабане с наполнителем;
б) промывка в горячей воде при температуре 70—90° С;
в) химическая очистка в 25-процентном растворе нитрита натрия при температуре 50—70° С;
г) промывка в горячей воде при температуре 70—90° С;
д) промывка в холодной проточной воде;
е) пассивация в 10-процентном растворе нитрита натрия при температуре 50—70° С.
Шлифование пластинок. По техническим требованиям (ГОСТ 4872—65) глубина выкрашивания на рабочих кромках пластинок не должна превышать 0,2 мм, а на нерабочих — 0,5 мм. Кроме того, ГОСТ 2209—66 допускает вогнутость и выпуклость по широким опорным поверхностям пластинок в пределах 0,05—0,2 мм.
Для многих режущих инструментов такое отклонение от плоскости недопустимо, и пластинки перед напайкой или механическим закреплением шлифуют абразивными, алмазными кругами или доводят карбидом бора. На некоторых заводах пластинки шлифуются химико-механическим способом [13].
Пластинки твердого сплава шлифуют на плоскошлифовальиых станках абразивными кругами КЗ или алмазными. Во избежание возникновения трещин па пластинках толщина слоя, снимаемого за один проход, не должна превышать 0,007 мм.
Пластинки шлифуются в приспособлении — рамке. В рамку одновременно помещают до 100 пластинок и заливают их сплавом воска с канифолью. Приспособление с пластинками устанавливают на магнитный стол станка.
После шлифования пластинки обезжиривают в кипящем 10—12-процентном растворе кальцинированной соды, затем промывают в горячей воде и подвергают пескоструйной обработке. Затем пластинки в течение 10 мин кипятят в 20—25-процентном растворе смеси буры с фтористым калием. После сушки пластинки покрывают тонкой стеклообразной пленкой флюса, которая предохраняет их от окисления до напайки и в процессе напайки.
Посадочные поверхности твердосплавных коронок — коническое отверстие и торец со стороны паза — должны быть шлифованными. Обработку отверстия коронки осуществляют химико-механическим способом, исправляя эллипсность, доходящую в некоторых случаях после спекания до 0,5 мм. С этой целью коронку 2 (рис. 37) устанавливают в медной ванне, причем коронка должна свободно входить в гнездо планки 3.
Во время обработки надо последовательно через 4—5 сек выводить медный притир из отверстия коронки и вводить его до контакта с отверстием. Это дает возможность свежей суспензии раствора медного купороса с абразивным зерном периодически поступать на обрабатываемую поверхность.
Для того чтобы абразивные зерна не оседали на дно ванны, в процессе работы происходит взмучивание суспензии лопатками, закрепленными на державке притира.
Обработка осуществляется при скорости вращения притира 10— 15 м/мин. Съем твердого сплава составляет в среднем 0,04—0,06 мм/мин на диаметр.
Подготовка многогранных пластинок. В настоящее время на заводах машиностроения широко применяют режущие инструменты, оснащенные круглыми и многогранными неперетачиваемыми пластинками. Перед сборкой эти пластинки проходят операции сортировки и доводки.
Сортировка пластинок. При изготовлении торцовых фрез, расточных головок и других многолезвийных инструментов, оснащенных многогранными пластинками, необходима предварительная сортировка их по основным размерам, влияющим на биение инструмента.
Биение главных режущих кромок у торцовых фрез с шестью-, пятью- и четырехгранными пластинками на двух смежных зубьях должно быть не более 0,12 мм,а суммарное биение — не более 0,2 мм. Торцовое биение допускается не более 0,2 мм.
Точные многогранные пластинки для черновых фрез целесообразно сортировать по схеме, приведенной на рис. 38. Пятигранная пластинка 2
поджимается двумя гранями к сторонам угла закрепленного шаблона 3, и по положению стрелки на шкале индикатора определяется партия, в которую попадает измеряемая пластинка. Угол шаблона соответствует углу при вершине пластинки.
Для исключения отдельных факторов, влияющих на точность сортирования пластинок, их следует поджимать в угол шаблона средней частью по толщине (см. сечения А— А и Б—Б), а не кромками верхнего или нижнего торца. Отклонение размера а отсортированных пластинок в пределах одной партии не должно превышать 0,05—0,08 мм.
Металлизация пластинок.
Металлизация опорных поверхностей минералокерамических пластинок позволяет напаивать их в открытый паз державок инструмента твердыми припоями. Прочность такой напайки (сопротивление сдвигу) достигает 900 кГ/см2.
Процесс металлизации пластинок заключается в следующем. Проверенные с помощью дефектоскопа пластинки промывают сначала в мыльной, а затем в чистой горячей воде. После просушки пластинки обезжиривают в ацетоне и покрывают пастой, состоящей из титана (или гидрида титана) и 3-процентного раствора целлулоида в амилацетате. Пасту наносят на поверхность пластинок кистью, а затем пластинки в количестве 200—300 шт. укладывают на противни для просушки. После просушки пасты на пластинки накладывают кусочки медной фольги толщиной 0,1—0,15 мм, загибая края фольги на торцы пластинки.
Противень с пластинками помещают в баллон, в котором создают вакуум примерно 2* 10-2мм рт. ст. Баллон помещают в электропечь, включают ее и нагревают до температуры 1100—1150° С, при которой медь плавится с титаном.
После охлаждения баллона пластинки вынимают и подвергают пескоструйной очистке для снятия налета, образовавшегося в процессе сплавления меди с титаном.
Изготовление инструмента из пластифицированных заготовок
Несмотря на преимущества твердых сплавов, почти все фасонные инструменты изготовляются из быстрорежущей стали, так как изготовление фасонного твердосплавного инструмента связано с большими трудностями.
Всесоюзный научно-исследовательский институт твердых сплавов (ВМИИТС) разработал новый способ изготовления фасонного твердосплавного инструмента, заключающийся в следующем. Методы порошковой металлургии изготовляют особый полуфабрикат — пластифицированные заготовки, легко поддающиеся обработке на металлорежущих станках. Обработкой резанием можно придать пластифицированной заготовке почти любую форму. После механической обработки «сырые» детали подвергают спеканию, благодаря чему они приобретают свойства твердого сплава.
Заготовки выпускают в виде сплошных дисков, колец, цилиндров, стержней и плиток различных размеров.
Пластифицированные заготовки обрабатываются твердосплавными инструментами. В частности, фрезерование заготовок лучше производить твердосплавными фрезами, которые изготовляются из пластифицированных заготовок твердого сплава марок ВК6М и ВКЮ.
Геометрические параметры режущих инструментов, предназначенных для обработки пластифицированных заготовок, следующие. Задний угол у резцов и фрез увеличен до 20—25°; такое увеличение заднего угла позволяет уменьшить налипание стружки и абразивный износ инструмента по задней поверхности; передний угол увеличивают до 20—30°, уменьшая тем самым угол заострения до 35—50°. Такие углы заточки снижают усилие резания и уменьшают вероятность сколов заготовки.
При обработке заготовок важно точно учитывать величину их усадки при последующем спекании. Коэффициент усадки указывается в паспорте, которым завод-изготовитель снабжает каждую партию пластифицированных заготовок; он колеблется в пределах 1,23—1,29.
По данным ВНИИТСа, форма пластифицированных заготовок при спекании искажается незначительно.
Технологический процесс изготовления режущих инструментов из пластифицированных заготовок состоит из механической обработки и спекания.
Процесс спекания производится в два приема:
1) предварительное спекание, во время которого удаляется парафин и происходит некоторое упрочнение детали;
2) окончательное спекание при температуре 1390° с целью формирования заданной структуры твердого сплава. При спекании происходит усадка, сплав уплотняется и приобретает нормальные качества.
Таким путем могут быть изготовлены различные режущие инструменты: фрезы, зенковки, развертки, фасонные дисковые резцы и т. п. Для режущего инструмента применяются заготовки из сплавов ВК6М и ВКЮ, но можно изготовлять инструмент и из других марок сплава.
В настоящее время ВНИИТСом организован производственный выпуск пластифицированных заготовок. При отпуске заготовок выдается обязательство осуществить спекание обработанных «сырых» инструментов.
На некоторых заводах, применяющих пластифицированные инструменты в значительном количестве, процесс спекания производится па месте.
Изготовление дисковых резцов. Фасонные дисковые резцы из пластифицированных заготовок нашли широкое применение в часовой промышленности при обработке колец корпуса. Технологический процесс изготовления дисковых резцов (рис. 42) состоит из следующих операций: