Конструирование литьевых форм в 130 примерах
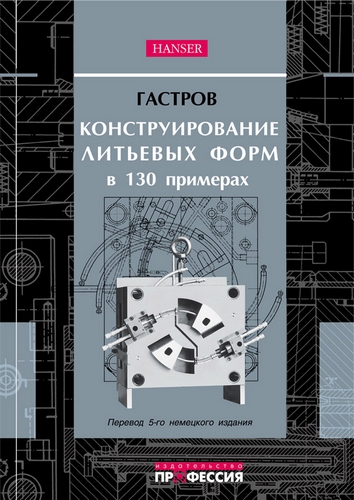
Гастров.
Профессия, 2006 г.
1.1 Виды исполнения форм для литья под давлением
Стандарт DIN 16750 «Пресс-формы и литьевые формы» предусматривает разделение форм по следующей схеме:
— стандартные формы (двухплитные формы);
— формы с ползунами (кассетные формы);
— формы с плитой съема;
— трехплитные формы (с двумя плоскостями разъема);
— многоэтажные формы;
— горячеканальные формы.
В целом, литьевые формы служат для переработки
— термопластов;
— реактопластов;
— эластомеров.
По аналогии с горячеканальными формами для литья под давлением термопластов имеются холодноканальные формы для литья реактопластов и эластомеров.
Если литниковые каналы по плоскости разъема не возможны или отливка должна быть расположена в многогнездной (многорядной) форме центрально, то для извлечения затвердевших литников потребуется вторая плоскость разъема (трехплитная форма) или подвод расплава через систему горячих каналов. У многоэтажных форм практически друг за другом соединены две формы в направлении смыкания, без необходимости в удвоенном усилии смыкания. Условием для создания таких форм являются большие объемы производства относительно простых, например, плоских изделий. Отличительным преимуществом считаются низкие издержки производства. В настоящее время все многоэтажные формы оснащаются горячеканальными литниковыми системами, к которым предъявляются высокие требования — особенно в части теплового баланса (термическая однородность).
Для извлечения отлитых изделий используются преимущественно цилиндрические толкатели. Зачастую они выполняют также дополнительную функцию вентиляции полостей. С тех пор как вертикальная электроэрозионная обработка стала нормой, проблемы вентиляции вышли на передний план. Если раньше формующие полости «строились» из многих элементов с возможностью эффективной вентиляции по соответствующим плоскостям разъема, то сегодня во многих случаях путем вертикальной электроэрозионной обработки возможно изготовление полостей из одного массивного блока. Поэтому следует особо позаботиться о том, чтобы расплав мог полностью вытеснять воздух. Необходимо также наверняка исключить включения воздуха — особенно в тех местах, которые оцениваются как критичные. Плохо вентилируемая полость может привести к созданию воздушных «карманов-ловушек» в изделии, образованию нагара (так называемый «эффект Дизеля») и даже к проблемам коррозии. Величина вентиляционного зазора зависит в основном от вязкости расплава. Ширина зазора находится обычно в диапазоне между 0,01 и 0,02 мм. У крайне высокотекучих полимерных материалов для избежания появления облоя зазоры необходимо уменьшать вплоть до 0,001' мм, но при этом увеличивается возможность образования «гусиной кожи». Следует учитывать, что там, где предусмотрены элементы вентиляции, эффективное термостатирование не всегда возможно. Элементы вентиляции, как, например, вентиляционные вкладыши из металло-керамических сплавов, требуют регулярного ухода из-за засорения пор в зависимости от времени эксплуатации и перерабатываемого материала. Расположение элементов вентиляции в полости должно выбираться с особой тщательностью.
Подвижные детали формы должны направляться и центрироваться. Направляющая колонна подвижной плиты литьевой машины должна в любом случае рассматриваться как приблизительное центрирование. В каждом случае необходимо индивидуальное центрирование литьевой формы.
Литьевые формы изготавливаются, как правило, из инструментальной стали. Выбор материала должен осуществляться очень тщательно, в соответствии с подлежащими переработке полимерными материалами. Требованиями к инструментальной стали, среди прочего, являются:
— высокая износостойкость;
— высокая коррозионная стойкость;
— высокая стабильность размеров и т. д. (см. раздел 1.9).
Возрастающий интерес проявляется, кроме этого, к формам из алюминиевых сплавов, как например AlZnMgCu 1,5, которые, среди прочего, характеризуются:
— незначительным весом;
— хорошей обрабатываемостью резанием;
— высокой коррозионной стойкостью;
— высокой теплопроводностью (возможность сокращения времени цикла);
— хорошей эрозионной обрабатываемостью.
1.2 Виды литниковых каналов и впускных литников
1.2.1 Холодноканальные системы
Согласно DIN 24450, различаются:
— литник, как часть отливки, не являющийся элементом формованного изделия;
— литниковый канал (разводящий литник) — от места входа расплава в литьевую форму до впускного литника;
— впускной литник является конечной частью литниковой системы (уменьшенного сечения), которая непосредственно подходит к формующей полости.
Путь расплава до полости должен быть максимально короток, чтобы, среди прочего, свести к минимуму потери давления и тепла. Вид и расположение разводящих/впускных литников имеют значение для:
— экономичного изготовления изделий;
— свойств отлитого изделия;
— допусков;
— линий спая;
— внутреннего напряжения и т. д.
Ниже дается обзор самых распространенных видов холодноканальных литниковых систем.
• Центральный (или пальчиковый) литник (рис. 1.2)
Применяется, как правило, для относительно толстостенных изделий или для термически щадящей переработки высоковязких расплавов. Центральный литник удаляется после выталкивания отлитого изделия из формы.
• Впускной точечный литник (рис. 1.3) Этот литник отрывается, как правило, автоматически. Если небольшие остатки литника вызывают помеху, тогда в линзообразное углубление на поверхности отливки можно вложить «<i». Для автоматического выталкивания конической части литника с впускным точечным литником или без него служат обычные промышленные так называемые пневматические сопла.
• Зонтичный литник (рис. 1.4)
Для изготовления, например, опорных втулок с высокими требованиями к радиальному биению с дополнительным исключением линий спая используют зонтичный литник. Недостатками являются одностороннее крепление оформляющего знака и необходимость для удаления литника применять обработку, дающую стружку. • Дисковый литник (рис. 1.5)
Применяется предпочтительно для цилиндрических отливок с впуском с внутренней стороны без линий спая. При переработке материалов с волокнистыми армирующими наполнителями дисковый литник уменьшает возможность деформации отлитого изделия. Литник должен удаляться после извлечения из формы.
• Щелевой литник (рис. 1.6)
Чтобы получить плоские отливки с незначительной деформацией и незначительным внутренним напряжением, рекомендуется использовать щелевой литник, который при ширине, равной ширине отливаемого изделия, ведет к выравниванию фронта потока. Определенное опережение потока в зоне центрального литника можно компенсировать корректировкой сечения литникового канала. Расположение впускного литника в одногнездной форме не по центру симметрии может привести к появлению облоя в форме из-за неравномерного заполнения формующей полости1. Как правило, щелевой литник срезается вне формы, что упрощает ее конструкцию. При необходимости литник можно отделить автоматически в форме в момент ее раскрытия. Это позволяет полностью автоматизировать цикл изготовления изделия.
• Туннельный впускной литник2 (рис.1.7)
В зависимости от компоновки впускной литник отделяется от изделия в процессе размыкания формы или в момент выталкивания через заданную кромку среза. Впускной туннельный литник в одной полуформе подходит для бокового впуска. За исключением возможных проблем в результате преждевременного отверждения материала в литниковом канале впускные туннельные литники могут быть очень малого поперечного сечения, что позволяет получать на изделии малозаметные следы. Кроме того, у полимерных материалов с абразивными, а также коррозионными характеристиками, кроме того, следует принимать во внимание повышенный износ кромки среза. С этим связаны также проблемы отрыва.
Литниковые каналы желательно выполнять предельно короткими, при этом необходимо, чтобы (независимо от места впуска) обеспечивалось равномерное и одновременное заполнение формующих полостей у многогнездных форм (при условии одинаковых гнезд), и каждая полость располагала равным по продолжительности временем выдержки под давлением. Звездообразные или кольцеобразные литниковые системы (рис. 1.8) имеют преимущество равной и кратчайшей длины литникового пути. Их недостаток, однако, проявляется в том случае, если, например, необходимо предусмотреть применение ползунов. Здесь рекомендуются рядные разводящие литники (рис. 1.9, а), имеющие неравные литниковые пути. Этот недостаток можно компенсировать за счет искусственной балансировки, например, с помощью компьютерного анализа в программе Mold/low. При этом варьируются диаметры литниковых каналов, но не сечения соответствующих впускных литников. Такой естественным образом сбалансированный кольцевой разводящий литниковый канал показан на рис. 1.9, Ь. Следствие подобной компоновки — относительно неблагоприятное соотношение объема отливаемого изделия к объему литниковых каналов.
1.2.2 Горячеканальные системы
Горячеканальные системы обеспечивают так называемый «6езлитниковый»способ литья под давлением изделий из термопластов. Они могут также успешно применяться как секционные обогреваемые каналы, то есть со вспомогательными разводящими литниками. При правильном исполнении в горячеканальных системах можно достичь значительно меньших потерь давления, чем в формах с затвердевающими литниковыми каналами.
Рациональная отливка изделий в многоэтажных формах стала возможной только при условии применения горячих каналов.
При полном исключении холодных разводящих каналов можно лучше использовать рабочий объем литьевой машины. С этим связано и сокращение времени заполнения формующей полости, а следовательно, сокращение времени цикла, однако не слишком существенное.
Принципы конструирования различных горячеканальных систем сильно различаются. Это относится как к коллекторам, так и к соплам (инжекторам) горячеканальной системы, форма и исполнение которых могут иметь существенное значение для характеристик отливаемого изделия (табл. 1).
Соответствующие горячеканальные литниковые системы не обязательно пригодны для переработки всех термопластов в равной степени, хотя время от времени это и утверждается. Как особый критерий следует выделить широкую термически щадящую переработку расплава.
Это предполагает использование достаточно затратных с точки зрения теплотехники принципов конструирования. В этом отношении горячеканальные литниковые системы, соответствующие требованиям, более затратны, прецизионны и иногда более чувствительны к помехам, чем обычные литьевые формы. В остальном для изготовления таких форм в особой мере действуют правила точности, свойственные для тонкой механики. Для переработки абразивно и/или коррозионно действующих полимерных материалов горячека-нальная литниковая система должна оснащаться соответствующим образом. При необходимости следует учитывать, например, несовместимость расплавов при контакте с медью и медными сплавами, что может привести к каталитическим явлениям распада. Сегодня поставщиками предлагаются соответственно оснащенные системы. Из-за более лучшего температурного режима предпочтение следует отдавать регулируемым горячеканальным литниковым системам по сравнению с управляемыми без обратной связи.
У литьевых форм среднего и особенно крупного размеров с соответствующе большими горячими коллекторами с успехом используется «естественная» или «искусственная» балансировка каналов для выравнивания давления. При «естественной» балансировке длина литниковых каналов в системе выбирается в основном равной. При «искусственной» балансировке цель достигается путем соответствующего изменения сечений разводящих литниковых каналов. Естественная балансировка имеет преимущество независимо от таких параметров переработки, как, например, температура и скорость впрыска, но означает, однако, усложнение коллектора, если расплав должен распределяться на несколько этажей. Оптимальная горячеканальная система должна обеспечивать полную замену расплава в минимальное время, так как расплавы в застойных зонах подвержены термической деструкции, что приводит к ухудшению характеристик отлитого изделия.