Кружева из металла
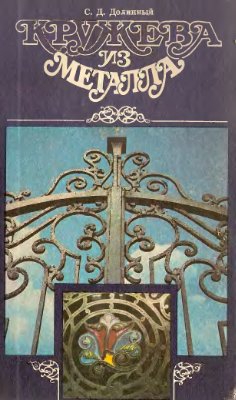
Долинный С.Д.
Киев, Урожай, 1991 г.
СВАРКА
Неразъемные соединения, применяемые в художественной обработке металла, можно условно разделить на три основные группы — сварные, паяные и клепаные.
Обычно предпочтение отдают первым двум, поскольку швы, полученные сваркой или пайкой, в дальнейшем можно так зачистить, зачеканить или обработать другим способом, что соединение не будет заметно и изделие, собранное из нескольких элементов, будет иметь вид единого целого. Кроме, конечно, тех случаев, когда соединение выполняет еще и функцию декоративного элемента. Например, хомуты и декоративные заклепки, применяемые при соединении кованых элементов.
Наиболее простое соединение черных металлов получают с помощью электросварки. Изобретенный в конце XIX в. способ соединения металла дуговой сваркой плавящимся электродом получил широкое распространение и являлся в свое время прогрессивным технологическим способом, применяемым в художественной обработке металла.
В качестве источника тока для получения сварочной дуги используют сварочные аппараты. При соединении деталей в художественной ковке обычно применяют электроды диаметром не более 3 мм. В связи с тем, что сила тока, необходимая для сварки, составляет 30—40 А на I мм диаметра электрода, то для этих целей вполне пригодны бытовые сварочные аппараты с максимальным рабочим током 80—100 А. Стремиться к увеличению или уменьшению силы тока не стоит, так как при больших, чем необходимо, токах металл электрода будет разбрызгиваться и получится некрасивый широкий шов. При этом электрод может значительно нагреваться, что приводит к отлущиванию его обмазки, а при сварке тонких листов металла или мелких элементов — к сквозному прожиганию их.
При малых токах затруднено зажигание дуги и отсутствует стабильность ее горения, что приводит к образованию неравномерного сварочного шва и неглубокому провару металла. После зачистки такого шва соединение может разрушиться.
Наибольшую допустимую силу тока выбирают при сварке в нижнем положении, при сварке в верхнем — силу тока уменьшают на 20—30 %.
При отсутствии электродов заводского изготовления их можно сделать самому, причем любого диаметра. Для этого на отрезок проволоки из малоуглеродистой стали для стабилизации дуги наносят обмазку, состоящую из 15 % жидкого натриевого стекла и 20 % мела, компоненты смешивают и доливают воду до консистенции сметаны.
Покрытие наносят, окуная заготовки в обмазку. Толщина ее не должна превышать 0,5 мм. Обычно диаметр таких самодельных электродов 1,5—2,5 мм. Их целесообразно применять при сварке изделий, состоящих из мелких элементов.
При отсутствии сварочного аппарата соединить стальные детали можно с помощью термитных электродов, хотя их использование и дает не очень красивое соединение. Однако из-за своей простоты этот способ применяют при монтаже секций ограждения, ворот и других металлоконструкций.
Основой термитного электрода является также отрезок проволоки из малоуглеродистой стали, на который наносят обмазку из смеси опилок алюминия и железной окалины (соответственно 23 и 77 %). Можно использовать только опилки из чистого алюминия, а железную окалину получить самому, нагрев стальную заготовку в горне и очистив металлической щеткой образовавшийся слой. В другом случае стальную мелкую стружку или опилки прожаривают в электрической муфельной печи или горне до их полного окисления. Смесь алюминиевых опилок с железной окалиной замешивают на декстриновом клее, но лучше во избежание отсырения — на любом нитроцеллюлозном.
В связи с тем, что скорость горения термита зависит от размера зерен компонентов обмазки (чем зерна меньше, тем быстрее происходит горение), размер их должен быть не менее 0,5 мм. При этом температура в зоне горения достигает 3000 °С.
Для придания цилиндрической формы электродам изготавливают трубочки из плотной бумаги такой же длины, как и отрезки проволоки. Затем полученные цилиндры заполняют термитной смесью, в них вставляют проволочную заготовку и сушат. Для воспламенения. термитного электрода необходимо конец его нагреть до температуры 1000 °С. Поэтому на конце электрода делают затравку, состоящую из одной части по массе бертолетовой соли и 0,5 части алюминиевых опилок. Поскольку не всегда представляется возможным приобрести бертолетовую соль, в качестве затравки можно использовать тонкую полоску магния, часть которой заформовывают в трубку вместе с термитной смесью. Оставшийся конец магниевой полоски поджигают перед началом работы. Магний служит запалом для термита, так как имеет высокую температуру горения. Термитную смесь можно также поджечь бенгальским огнем, дающим высокую температуру.
При формовке термитного электрода необходимо оставить небольшой оголенный конец проволоки, за который его можно будет удерживать плоскогубцами. Удобно для этих целей использовать держатель типа электросварочного. Работать необходимо в темных очках и рукавицах.
Сварка меди, латуни и алюминия. В условиях мастерской медь сваривают газосваркой. Однако в связи с тем, что она имеет высокую теплопроводность, необходим повышенный расход газовой смеси, а при сварке медных заготовок большой массы — их предварительный подогрев. Поэтому в домашней мастерской целесообразно применять сварку для меди толщиной не более 2 мм. Сварку листов производят встык. В качестве флюса используют соединения бора — буру, борную кислоту, борный ангидрид или смесь прокаленной безводной буры и борной кислоты.
Приведем несколько составов флюсов для сварки меди, %:
1.Бура 30, борная кислота 50, поваренная соль 10, кислый фосфорнокислый натрий 10.
2.Бура 70, борная кислота 10, поваренная соль 20
3.Бура 50, борная кислота 50
Флюс в виде пасты наносят на очищенные кромки металла.
Широко применяется способ, когда нагретый конец присадочного прутка окунают во флюс, а затем переносят в зону сварки. В качестве присадки используют полоски меди или медную проволоку. При сварке латуни в качестве флюса используют те же составы, что и при сварке меди. Металл толщиной до 1 мм сваривают с отбортовкой кромок, которые предварительно очищают до блеска.
Алюминий также можно сварить плавлением, используя газовую горелку. Перед сваркой кромки алюминиевых заготовок тщательно зачищают и при малых толщинах металла отбортовывают. Обычно применяют специальные флюсы, растворяющие стойкую окись алюминия при низких темпратурах. Один из составов флюса содержит следующие компоненты, % по массе: NaCl28, КО 50, ZiCl14, NaF8.
В связи с тем, что обязательным компонентом флюсов для сварки алюминия являются дорогие соли лития, которые домашний мастер не всегда может приобрести, сварку листового алюминия целесообразно заменить пайкой или выполнить клепаное соединение.
Толстостенные отливки из алюминия можно попытаться заварить без применения флюса. Для этого на кромках свариваемых деталей делают скосы. Плотно соединив детали, нагревают место соединения до тех пор, пока не расплавится поверхностный слой металла. Когда появятся складочки на месте нагрева, их удаляют стальным скребком, очищая металл от окисной пленки, и тут же вводят в пламя присадочный пруток, который сплавляют в образовавшуюся сварочную ванну. Этим же прутком стараются смешать расплавленный металл, постоянно удаляя окисную пленку. Если какие-то участки деталей не соединились, операцию повторяют.
ПАЙКА
Для пайки черных металлов в качестве припоя в основном используют латунь, кусочек которой кладут между соединяемыми деталями. Затем полученный пакет связывают стальной проволокой, помещают в горн и нагревают до расплавления латуни. Как только она расплавится, детали необходимо вынуть, так* как при перегреве латунь может вытечь из соединительного шва. Источником тепла может служить газовая горелка, тогда процесс пайки легче контролировать. Для пайки стали и меди используют медно-цинковый припой или латунь марки Л-62. Флюс — прокаленная бура.
При сборке тонких ажурных решеток соединение пайкой наиболее предпочтительно. Элементы кованой решетки укладывают на ровный асбестовый лист и места соединения тщательно зачищают. Далее место пайки нагревают и присыпают бурой. Когда металл детали достаточно нагреется, в пламя вводят присадочный пруток и оплавляют его конец до образования капли расплавленного металла. Нагрев продолжают до тех пор, пока металл припоя не заполнит зазор соединения. Так спаивают все точки соединения Латунь относится к группе твердых припоев с температурой плавления свыше 500 °С.
Для получения высококачественных паяных соединений используют также припои на основе серебра. Для пайки меди, латуни, стали и бронзы наиболее универсальным является припой марки ПСр 45, состоящий из следующих компонентов, % по массе: серебро 45, медь 30, цинк 25.
Температура начала плавления припоя 933 °С, полного расплавления 998 °С.
Для соединений, не несущих больших механических нагрузок, применяют мягкие низкотемпературные (температура плавления ниже 400 °С) оловянно-свинцовые припои, используемые при пайке меди, латуни и оцинкованной стали. Пайку названных металлов проводят обычным способом — паяльником или горелкой. В качестве флюсов применяют хлористый цинк, хлористый аммоний в порошке или кусках, чаще всего — раствор хлористого цинка с добавкой хлористого аммония. Раствор хлористого цинка получают, растворяя мелконарезанный цинк в технической соляной кислоте до прекращения реакции. Флюс с хлористым цинком используют следующего состава, %: хлористый цинк 25—50, хлористый аммоний (нашатырь) 5—20, остальное — вода. После пайки остатки флюса необходимо тщательно смыть.
Более качественное паяное соединение дают мягкие припои, содержащие небольшое количество серебра, следующего состава, %:
1.ПСр 3: серебро 3, свинец 97. Температура плавления 573—578 °С
2.ПСр 2: серебро 2, кадмий 5, олово 30» свинец 63. Температура плавления 498—508 °С
В связи с тем, что для качественной пайки алюминия требуются те же дорогие флюсы, что и для сварки его, рекомендуется применять более простой способ соединения — оловянно-свинцовыми припоями. Перед пайкой деталь необходимо залудить, удалив поверхностный слой - окиси алюминия. Для этого на нагретое до температуры пайки место наносят припой и растирают металлической щеткой или шабером. При растирании соскабливается поверхностный слой окисла и припой прочно соединяется с зачищенной поверхностью металла. Иногда вместо металлической щетки используют кусок войлока с абразивом. Если необходимо, в процессе растирания место подогревают и добавляют припой. Когда деталь хорошо залу-дится, ее паяют обычным способом.
Лудить алюминий будет значительно легче, если его предварительно омеднить. Хорошо зачищенное и обезжиренное место пайки ограждают бортиком из пластилина. В образовавшуюся емкость заливают насыщенный раствор медного купороса с добавлением капли спирта для лучшего смачивания. К алюминиевой детали подсоединяют отрицательный полюс источника постоянного тока, а к положительному полюсу — отрезок медной проволоки, конец ее опускают в раствор так, чтобы она не касалась детали. Через некоторое время на ней осядет тонкий слой меди, который промывают, сушат и лудят.
Данный способ применяют для пайки небольших деталей. Площадь осаждения меди не должна превышать 1 см2. Не следует наращивать толстый слой, так как в этом случае возможно его отслоение.
Если у домашнего мастера есть возможность приобрести соли лития, то пайку алюминия производят припоем П250А, содержащим 80 % олова и 20 % цинка. В качестве флюса используют смесь олеиновой кислоты и йодида лития. Йодид лития (2—3 г) помещают в пробирку или колбу и добавляют 20 мл (около 20 г) олеиновой кислоты. Смесь слегка подогревают, опустив пробирку в горячую воду, и перемешивают до полного растворения соли. Полученный флюс сливают в стеклянную посуду с плотной крышкой. При использовании водной соли лития ее также смешивают с олеиновой кислотой, при этом водная смесь опускается на дно, флюс всплывает наверх и его аккуратно сливают.
Перед пайкой хорошо очищенное жало паяльника лудят припоем П250А с канифолью. Соединяемые детали смачивают полученным флюсом и паяют. Остатки флюса смывают спиртом, ацетоном или бензином.
Следует отметить, что флюс в процессе пайки не выделяет токсичных веществ.
Алюминий толщиной до 2 мм паяют паяльником мощностью до 100 Вт. Пайка более толстого листа или деталей требует предварительного подогрева горелкой.
СОЕДИНЕНИЕ ДЕТАЛЕЙ РАСПЛАВЛЕННЫМ МЕТАЛЛОМ
Помимо газовой и электродуговой сварки, можно соединять металлы с помощью литейной сварки. Этот прием используют в основном для соединения деталей художественных отливок из меди, бронзы и латуни. Процесс сварки технологически сходен с производством отливок. Места соединения зачищают так, чтобы между соединяемыми деталями образовался зазор, величина которого зависит от формы и размера заготовок, но с таким расчетом, чтобы его легко мог заполнить заливаемый металл. Место сварки подготовленных деталей заформовывают, форму предварительно подогревают и стык заливают расплавленным перегретым металлом.
Таким же способом производят пайку, заливая место соединения соответствующим припоем. Предварительно места соединения необходимо залудить и покрыть флюсом.
Кроме использования расплавленного металла для сварки, возможно применение его для соединения деталей литыми заклепками. Для этого в соединяемых частях деталей в точке соединения сверлят отверстия. На одной из деталей, напротив отверстия, из гипсовой массы формуют головку заклепки, а на другой отверстие зенкуют. Детали соединяют до совмещения отверстий и заливают расплавленным металлом. Таким способом можно получать заклепки с любой формой головки.
При необходимости иметь головку заклепки с двух сторон готовят литейную форму с боковым литником, которую устанавливают на второй детали.
Во избежание прорыва металла через зазоры между формой и деталью их обмазывают гипсовой массой.
Головки впотай выполняют укладкой нижней детали на плоскую стальную плиту с предварительной глубокой зенковкой отверстий и с последующей заливкой расплавленного металла.
Сварку стали расплавленным металлом можно выполнять в условиях мастерской, если применить для этого термитную смесь. Выше уже был описан способ изготовления термитных электродов. Используя для термитной смеси те же компоненты, можно получить расплав черного металла.
Для получения I кг термитной смеси необходимо 230 г зерен алюминиевого порошка и 770 г железной окалины. При расчете необходимого количества смеси следует учесть, что выход расплавленной стали составит 500— 550 г, остальное — шлак.
Термитную смесь сжигают в шамотном тигле, размер которого выбирают в зависимости от количества смеси. Смесь поджигают с помощью сварочной дуги. После воспламенения тигель накрывают огнеупорной крышкой с отверстием для выхода газов. Процесс горения длится 20— 30 с. Затем снимают крышку, удаляют с поверхности расплава шлак и расплавленную сталь заливают в форму.
Данный способ можно применить не только для сварки расплавленным черным металлом, но и для отливки отдельных деталей.
При монтировке художественных изделий часто возникает необходимость получения такого соединения, при котором на одной из деталей не было бы заметно никаких следов. В данном случае поступают следующим образом: в детали, на которой требуется закрепить декоративный элемент, сверлят одно или несколько отверстий, детали прижимают одна к другой и через отверстия производят пайку или сварку до полного плавления присоединяемой детали с несущим элементом. При этом способе на присоединяемой детали не остается никаких следов.
Под электродуговую сварку отверстие должно быть в два раза больше, чем диаметр электродов, тогда место соединения не засорится шлаком и образуется хороший провар металла. В листовом металле толщиной до I мм отверстия не сверлят, а прожигают сварочной дугой в процессе сварки. Если необходимо, места сварки зачищают.