Заточка режущего инструмента
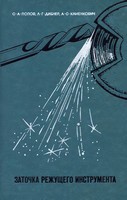
Попов С. А.
Высшая школа, 1970 г.
§ 2. МАТЕРИАЛЫ, ПРИМЕНЯЕМЫЕ ДЛЯ ИЗГОТОВЛЕНИЯ РЕЖУЩИХ
ИНСТРУМЕНТОВ
Для того чтобы режущая часть инструмента была способна внедряться в обрабатываемый материал и в течение длительного времени срезать с заготовки лишний слой (припуск), материал, из которого изготовляется режущая часть инструмента, должен обладать определенными свойствами.
В первую очередь инструментальный материал должен быть очень твердым и прочным. Эти свойства должны сохраняться и при нагреве материала в процессе резания до высоких температур, т. е. инструментальный материал должен обладать теплостойкостью (или красностойкостью).
Режущая часть инструмента должна быть способна сопротивляться истирающему воздействию обрабатываемого материала в течение продолжительного времени в условиях высоких давлений и нагрева, т. е. инструментальный материал должен обладать высокой износостойкостью.
Инструментальные материалы должны также обладать способностью обрабатываться при первоначальном изготовлении режущих инструментов и затачиваться в процессе их эксплуатации.
Все эти свойства зависят от химического состава, структурного состояния и физико-механических свойств инструментальных материалов.
Современные режущие инструменты изготовляются из углеродистых и легированных инструментальных сталей, быстрорежущих инструментальных сталей, твердых сплавов, минералокерамики, алмазов, абразивных материалов.
Углеродистыеи легированные инструментальные стали обладают высокой твердостью, прочностью и износостойкостью, но эти свойства сохраняются лишь при нагреве до невысоких температур (не свыше 200—300° С). Поэтому такие материалы применяют для резания сравнительно мягких, малопрочных материалов и обрабатывают с невысокой скоростью резания.
Для получения высокой твердости инструментальные стали имеют повышенное содержание углерода: от 0,7 до 1,4%. Они содержат также сравнительно небольшое количество других элементов, которые называют легирующими.
Введение в сталь легирующих элементов придает стали специальные свойства.
В настоящее время в качестве легирующих элементов используются хром, кобальт, никель, молибден, титан, вольфрам, бор, азот, алюминий, ванадий, цирконий, ниобий и др.
В инструментальных сталях количество легирующих элементов сравнительно невелико, обычно до 3—4%.
Углеродистые инструментальные стали в соответствии с процентом содержания в сталиуглерода делятся на марки: У7Л, У8А, У9А, У10А, У11А, У12А, У13А. Маркировка этих сталей расшифровывается так: буква У означает «углеродистая», следующая за буквой У цифра указывает содержание в стали углерода, выраженное в десятых долях процента, т. е. 0,7; 0,8; 0,9; 1,0; 1,1; 1,2; 1,3%. Буква А в конце маркировки указывает на то, что сталь высококачественная, т. е. содержит мало вредных примесей (серы и фосфора).
Легированные стали имеют также свою маркировку, причем каждый легирующий элемент обозначается определенной буквой:
Хром — X
Вольфрам — В
Алюминий — Ю
Никель — Н
Кремний — С
Титан — Т
Молибден — М
Ванадий — Ф
Цирконий — Ц
Марганец — Г
Ниобий — Б
Фосфор — П
Медь — Д
Азот — А
Содержание легирующего элемента (в процентах) указывается цифрами после буквы; если его содержание меньше или равно (в среднем) 1%, то после буквы цифра не проставляется. Так, хромо-кремнистая сталь 9ХС содержит 0,95—1,10% С (углерод); 0,95—1,25% Сr (хром); 1,20—1,60% Si(кремний). Иногда в марке содержание углерода не указывается: например, сталь Х12Ф1 содержит 11,0—12,5% хрома, 0,7—0,9% ванадияи 1,2—1,4% углерода.
В производстве режущих инструментов из инструментапьных легированных сталей наибольшее применение находят две стали: хромокремнистая 9ХС и хромовольфрамомарганцовистая ХВГ.
Если процент легирующих элементов в стали увеличить: вольфрама до 8,5—19%, хрома до 3,8—4,6%, а также ввести молибден и ванадий, то можно повысить теплостойкость до 600е С без существенного снижения стойкости. Такие стали называют быстрорежущими.
По сравнению с инструментами из углеродистой сталиинструменты из быстрорежущей стали допускают более высокую скорость резания при одинаковой стойкости.
Основной маркой быстрорежущей стали является Р18, которая содержит 17,5—19,0% W, 3,8—4,4% Сr, 0,7—0,8%С и 1,0—1,4%V.
Из этой стали изготовляют большинство режущих инструментов, так как в закаленном состоянии она обладает стабильными высокими режущими свойствами и весьма повышенной износостойкостью. инструменты из стали Р18 хорошо переносят ударные нагрузки при работе и их легко можно перетачивать по мере затупления и износа.
Многие инструменты делают составными: рабочая часть (принимающая непосредственное участие в резании) выполняется из быстрорежущей стали, а нерабочая (корпус, хвостовая часть и т. д.) — из менее дорогой — конструкционной стали.
Низковольфрамовая быстрорежущая сталь марки Р9 содержит 8,5—10% вольфрама, т. е. в два раза меньше по сравнению со сталью Р18, и 2—2,6% ванадия вместо 1,0—1,4%, что позволило почти выравнять режущие свойства, по привело к ухудшению ее шлифуемости. Поэтому при заточке вследствие повышенного содержания ванадия могут возникать прижоги — поверхностные дефекты, ведущие к понижению твердости. В последнее время широко стали использоваться быстрорежущие стали марок Р12 и Р6МЗ.
Помимо сталей нормальной производительности, применяются также быстрорежущие стали повышенной производительности.
Ванадиевая сталь Р9Ф5 имеет увеличенное содержание ванадия (до 4,3—5,1%) и углерода (до 1,4—1,5%) и обладает высокой износостойкостью в инструментах с небольшой толщиной стружки и малыми скоростями (развертки, метчики, протяжки и т. п.).
Быстрорежущие стали Р18Ф2 и Р14Ф4 с меньшим количеством ванадия (1,8—2,4% и 3,4—4,1% соответственно) занимают по своим свойствам промежуточное положение.
Кобальтовые быстрорежущие стали повышенной производительности Р9К5, Р9КЮ, Р18К5Ф2 и Р10К5Ф5 обладают более высокой износостойкостью, красностойкостью и твердостью по сравнению со сталью Р18 и могут применяться для изготовления инструментов, нагревающихся при работе до высоких температур (обработка нержавеющих, жаропрочных сплавов и сталей, а также при обработке легированных сталейтвердостью НВ 300ч-350). Кобальтовые стали используются при изготовлении фрез, резцов, сверл и других инструментов.
Инструментальные углеродистые и легированные стали после соответствующей термической обработки могут иметь твердость
HRC58—64. Твердость быстрорежущих сталей обычной производительностиHRC63—65, для быстрорежущих сталей повышенной производительностиHRC64—66.
Инструменты с низкой твердостью очень быстро изнашиваются и становятся неприспособленными для работы, так как теряют свою форму и размеры. С повышением твердости шлифуемость стали при изготовлении и при переточках ухудшается. Однако чрезмерное повышение твердости может вызывать преждевременное выкрашивание режущих кромок и быть причиной поломки инструмента.
В настоящее время для производства режущих инструментов очень широко используются твердые сплавы. Эти инструментальные материалы содержат чрезвычайно твердые и тугоплавкие металлоподобные вещества, называемые карбидами, нитридами, боридами и силицидами. Они представляют собой соединения углерода, азота, бора, кремния с металлами — вольфрамом, титаном, танталом, ниобием, молибденом. Температураплавлениякарбидов очень высокая в пределах 2000—3800° С, а по твердости они приближаются к самому твердому веществу — алмазу.
Твердые сплавы изготовляются по особому технологическому процессу, называемому порошковой металлургией. Порошкикарбидов смешиваются с порошками некоторых металлов, из них формируются и прессуются изделия или пластинки, которые затем подвергаются термической обработке — спеканию при температуре ниже температурыплавления исходных материалов.
Такой процесс позволяет получать инструменты и детали сложной формы, с особой структурой. Обычно это очень мелкозернистые соединения частиц карбидовразмером 0,5—10 мкм, соединенных цементирующей средой. Цементирующим металлом в твердых сплавах обычно являемся кобальт.
Использование для изготовления инструментов твердых металлокерамических сплавов позволяет существенно повысить производительностьобработки (почти в 2—3 раза) в основном за счет использования более высоких скоростей резания (до 150—200м1мин вместо 40—50 м/мин для инструментов из быстрорежущих сталей).
Теплостойкость твердых сплавов достигает 750—1100QС, а их Твердость находится в пределахHRA87—92, г. е. выше твердости быстрорежущей стали на 5—8 единиц по HRC.
В СССР стандартизовано три шкалы (В; С: А) измерения твердости на приборах типа Роквелла. При пользовании шкалой С алмазный конус внедряется в поверхность детали под нагрузкой 150 кГ, а при определении твердости деталей из твердых сплавов по шкале Анагрузка уменьшается до 60 кГ, так как большие нагрузки в этом случае могут повредить алмаз. При определении твердости по шкале Вберется стальной шарик и груз в 100 кГ. .
Для изготовления режущих инструментов применяются три группы твердых сплавов.
К первой группе относятся вольфрамовые однокарбидные сплавы типа ВК*(ВК2, ВКЗМ, ВК4, В Кб, ВК6М, В KB, ВК8В), представляющие сплавкарбидавольфрама с кобальтом, содержание которого колеблется в пределах от 2 до 8% и выше.
Процентное содержание кобальта указывается в обозначении сплава. Например, сплав ВК6М содержит 6% кобальта и 94% карбида вольфрама. Буква М обозначает, что сплав является мелкозернистым. Крупнозернистые сплавы этой группы имеют дополнительное обозначение — букву В (например, ВК8В).
Сплавы типа ВК в основном применяются для обработкичугуна и неметаллических материалов.
Ко второй группе относятся двухкарбидные титано-вольфрамовые сплавы типа ТК (Т5К10, Т14К8, Т15К6, Т30К4, Т5К12В), представляющие соединениякарбидоввольфрама и титана, сцементированных кобальтом. Эти сплавы менее прочны, чем сплавы типа ВК, но они имеют более высокую износостойкость при обработке деталей из различных видов стали.
В обозначении сплавов этой группы цифра, следующая после буквы Т, обозначает примерное содержание в сплавекарбида титана, а цифра после буквы К — содержание кобальта. Например, сплав Т15К6 содержит 15% карбида титана, 6% кобальта, а остальные 79% карбида вольфрама.
Сплавы третьей группы состоят из зерен карбида титана, карбида тантала, карбида вольфрама, сцементированных кобальтом, и называются титанотанталовольфрамовыми твердыми сплавами типа ТТК (ТТ7К12, ТТ7К15). Эти сплавы в основном также применяются для обработки резанием сталей.
Сплав ТТ7К12 содержит 12% кобальта, 3% карбида тантала, 4% карбидатитана и 78% карбида вольфрама.
Твердые сплавы для режущих инструментов применяются в виде стандартных пластинок определенных форм и размеров. Пластинки к корпусу или державке инструмента могут прикрепляться механически или посредством напайки.
Некоторые виды инструментов (прорезные и отрезные фрезы, сверла, фасонные резцы, фрезы канавочные, шлицевые, пальцевые, червячные) могут изготовляться и монолитными, т. е. целиком из твердого сплава.
Твердые сплавы, хотя и обладают высокой теплостойкостью, очень чувствительны к резкимколебаниям температуры, которые возможны как в процессе резания, так и при изготовлении инструмента (припайка, шлифование, заточка и т. п.).
При неправильном проведении этих процессов на твердом сплаве появляются трещины, которые могут быть как глубокими, так и поверхностными с незначительной глубиной проникновения. Титановольфрамокарбндные сплавы типа ТК более чувствительны к появлению трещин, чем вольфрамокарбидные сплавы типа ВК.
Теплопроводность сплавов типа ТК в 2—3 раза меньше теплопроводностисплавов типа В К. Теплоемкость твердых сплавов сравнительно мала и в 2—2,5 раза меньше теплоемкости быстрорежущей стали. Коэффициент линейного расширения твердых сплавов типа ТК почти в 2 раза меньше, чем для углеродистой стали, из которой изготовляются державки и корпуса. Поэтому из-за разницы в значениях коэффициентов линейного расширения пластинок твердого сплава и стальной державки при напайке могут возникать дополнительные напряжения, следствием которых является образование трещин, отслаивание пластинок.
С повышением в сплавахТК содержания карбидовтитана склонность к появлению трещин значительно возрастает.
Твердые сплавы обладают малой пластичностью и могут успешно работать только при постоянных нагрузках. При переменных нагрузках и вибрациях твердые сплавы выкрашиваются. Пластичность твердых сплавов уменьшается с уменьшением содержания в сплаве кобальта, однако их режущие свойства повышаются.